A Powerful Material From A Powerful Source Today’s Application Of Tungsten And Molybdenum
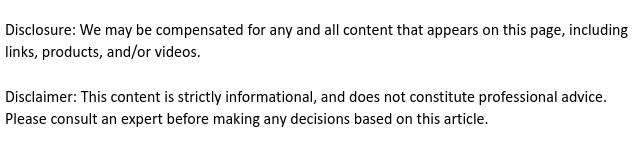
Knowing your metals inside and out will mean the difference between yielding success and missing out on golden opportunities.
It doesn’t matter if you’re just shuffling through new alloy products. Taking extra care to figure out why and how each metal stands out from each other is how you wring out every last bit of potential from your business model. A slight change in your furnace electrode can make your product last longer. Investing in molybdenum can change the way your customers think about your presentation, encouraging word-of-mouth. The little details all but define a business and that’s exactly what will be looked at in the list below.
From the molybdenum crucible to tungsten alloy machining, now is a great time to brush up why there’s no such thing as a one-size-fits-all in the world of metals.
History Of Tungsten
Your alloy product manufacturer has had a long time to perfect the art of tungsten. This material was first discovered over 235 years ago in the late 1700’s, but wasn’t applied to an industry for another 150 years. It only appears naturally when combined with the four major mineral forms, alongside calcium and iron. When it comes to metals in their purest form, tungsten has the highest melting point at over 6,000 degrees Fahrenheit. It also has the highest tensile strength and the lowest vapor pressure. These extreme numbers have gone a long way to cement it as irreplaceable in today’s market.
Tungsten Used Today
Today you can find tungsten in a wide variety of products and applications. With a tensile strength of 1,510 megapascals and more dense than steel, it won’t be replaced anytime soon. A tungsten carbide falls between a solid 8.5 and 9 on the Moh’s hardness scale, right behind diamonds who have a hardness of 10. Today it’s estimated there are only 1.25 grams of tungsten per 1,000 kilograms of the Earth’s crust, making it highly coveted among several manufacturers trying to find the highest amount of quality for their clients.
History Of Molybdenum
Where tungsten is incredibly hard and can withstand high temperature counts, molybdenum offers a slightly different variety. This material has a high melting point of nearly 4,800 degrees Fahrenheit and was recognized as an official element around the same time tungsten was. It’s been used for several purposes since then, ranging from the furnace electrode to general glass melting electrodes. In order to reach this amount molybdenum must have purity levels of nearly 100% to have the right resistance to chemical corrosion.
Molybdenum Used Today
Where there is a molybdenum manufacturer, there is a furnace electrode providing incredible quality and durability. Vacuum furnaces capable of temperatures beyond 2,000 degrees Fahrenheit are used in medical, crystal growth, and electronics industries. Constant heat transfers and pressure differences mean quality can’t be ignored if a product is to enjoy a long lifespan. Taking another look at your glass melting electrodes and comparing them with today’s furnace electrode could be the first step toward sending out a better result.
Making The Difference In Your Products
Now for a review. Replacement furnace parts should be high on your shopping list. Metals aren’t required to just be durable or affordable, but flexible enough to withstand changes in pressure and complex enough to encourage seamless heat transfers. Tungsten and molybdenum, despite their differences in melting point, have a similar history of discovery and application today. The custom vacuum furnace and its furnace electrode can hold up for years thanks to the ingenuity of hard-working manufacturers and scientists keen on bringing out the best in today’s materials.
There’s always more to learn. Apply your knowledge to your crucibles and start the transformation now.