Boroscope Inspections for Gas Turbines Maximize Safety and Efficiency
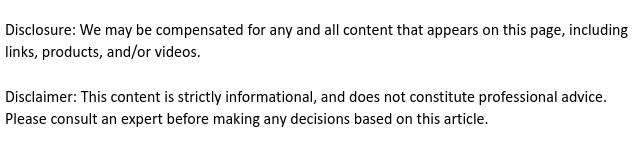

Natural gas is the second most important source of energy in the U.S. Gas fired power plants use gas turbines to generate electricity. New designs make gas turbines highly efficient, achieving fuel to energy conversions of 60%. Regular inspections are essential to keeping gas turbines running at peak efficiency. Turbine inspections using boroscopes can be used to determine if repair work or maintenance is needed, preventing major problems.
Natural gas is the second most important fuel
The U.S. is the leading producer of natural gas in the world, with the annual output reaching 750 billion cubic meters in 2016. Natural gas is the second most important energy source in the country. One of its leading applications is in the field of power generation. Natural gas-fired power plants use gas turbines, which are related in design to the steam turbines that have been used since the 1880s to produce electricity.
Gas turbines are much larger and heavier than steam turbines, and consist of three main sections: the compressor, the combustion system and the turbine. The compressor feeds pressurized air to the combustion chamber at very high speeds, reaching hundreds of miles an hour. In the combustion chamber, the air is mixed with fuel and burned to reach temperatures of 2000F. The heated mixture then moves through the turbine sections, where it expands and rotates the turbine blades, generating electricity.
Achieving higher efficiency for gas turbines
The limits to fuel to energy conversion efficiency in gas turbines are defined by the temperatures that can be tolerated within the turbines. The Department of Energy, through its advanced turbine program, has designed turbines that can achieve energy efficiency levels of 60%, as compared to the 20 to 35% achieved by simpler models.
Designs that can capture waste heat for industrial purposes or heating can further improve energy conversion levels to 80%. Regular repair and maintenance and turbine inspections are essential for safety and peak efficiency. In particular, the build up of salt particles can reduce efficiency by as much as 15%. Visual and non destructive gas turbine inspections using boroscopes can help to prevent this loss.
Borescope inspections and safety
Borescope inspection of gas turbines is essential to safety and maintenance. They can help to determine if and when maintenance and repair work is needed. A boroscope conducts a visual inspection of a gas turbine, inspecting the interior surface for burrs, holes and irregularities in the finish. A boroscope inspection report is an important part of the safety and maintenance procedures for gas turbines.
Sometimes boroscopes can be fitted with video or imaging devices, which can transmit images of the interior to be inspected. Turbine inspections are essential to keep them running safely and at peak efficiency.
Turbine support services like boroscope and nondestructive turbine inspections can keep gas turbines running safety and at maximum efficiency. Regular inspections can be used to determine when and if repair and maintenance work is needed, avoiding expensive and time-consuming shut downs for servicing.