How to Prevent Inventory Shortage in Eight Different Industries
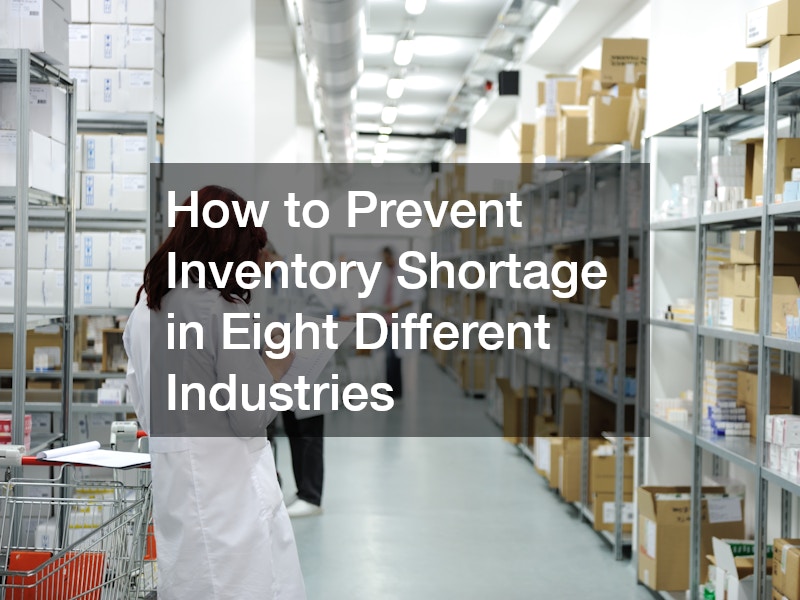
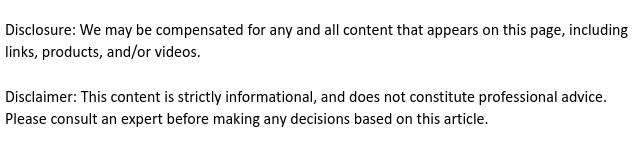
Introduction
In recent years, various sectors have been experiencing significant inventory shortages. These shortages have been attributed to various factors including supply chain disruptions, increased demand, and manufacturing delays. As industries adapt to new norms, these shortages present substantial challenges that impact both businesses and consumers. This article delves into the specifics of inventory shortages across a diverse range of industries. We will explore the consequences and adaptations required in sectors such as medical services offering PDO threads and Botox, auto repair shops, truck dealerships, pool service teams, and more. The primary keyword ‘tbd’ will guide us through the intricate details and far-reaching implications of these shortages. We will also touch upon the impact on custom adhesive products, florists providing flowers, carbon steel products, and companies selling new golf carts. Through this extensive discussion, we aim to provide insights into how businesses are navigating these turbulent times and what the future may hold for various sectors.
PDO Threads and Inventory Shortage
PDO threads are a popular choice for non-surgical facelifts in the cosmetic industry. However, the supply chain disruptions have made it difficult for clinics to maintain an adequate inventory of these threads. This shortage has forced many businesses to limit the number of procedures they can perform, thus affecting their revenue and client satisfaction. The increased demand for such aesthetic treatments hasn’t matched the supply, leading to operational challenges.
Many clinics that offer PDO threads have had to search for alternative suppliers, often at higher costs. This has not only affected the clinics financially but also posed risks of quality compromises. The tbd fluctuation in cost and availability of PDO threads can result in lesser accessibility for clients who seek these affordable alternatives to surgical procedures. Consequently, clients must endure longer waiting periods or seek other cosmetic solutions.
The shortage of PDO threads signifies a broader issue affecting the cosmetic industry. It underscores the vulnerabilities in global supply chains, especially for specialized medical products. Unpredictable disruptions and delays in obtaining stocks mean that precise planning and risk mitigation strategies must be implemented. For businesses looking to maintain their tbd client base and service offerings, staying informed and agile is crucial.
Botox Services and Inventory Shortage
Botox services are essential for many clinics catering to clients seeking anti-aging and aesthetic treatments. The rise in demand for Botox services coincides with a global inventory shortage that affects the entire supply chain. Medical professionals are increasingly under pressure to source genuine and effective Botox products, which has been challenging due to bottlenecks in production and logistical constraints.
The shortage has led to competition among clinics, each striving to secure enough Botox to meet client needs. This competitive environment has consequently pushed up the prices of available supplies. As Botox services become more expensive, clients must either bear the higher costs or wait until the inventories stabilize. tbd Ensuring the availability of Botox services without compromising quality or affordability is a balancing act that many clinics are struggling with.
Long-term strategies are needed to address these inventory challenges in the Botox service industry. Enhanced collaborations with suppliers, diversifying sources, and adopting forecasting technologies may provide some buffer against future shortages. These strategies will contribute to sustaining client trust and retaining market share, even amidst unpredictable tbd supply chain dynamics.
Truck Dealerships and Inventory Shortage
Truck dealerships are crucial in ensuring the logistics and transportation industries operate smoothly. Yet, they have faced severe inventory shortages mainly due to supply chain disruptions and microchip shortages that halt production lines. These shortages mean that many dealerships struggle to meet the demands of their customers, leading to significant delays in deliveries.
Many truck dealerships are experiencing a backlog of orders, with long waiting periods becoming the norm. Customers who rely on these trucks for their businesses find themselves at a disadvantage, having to either prolong the use of older vehicles or rent alternatives, which may not always be feasible. This backlog represents a substantial bottleneck in crucial sectors such as freight and logistics where tbd truck availability is paramount.
To mitigate these challenges, some truck dealerships have started exploring partnerships with multiple suppliers and considering alternative financing options to maintain some level of inventory. By spreading risks and developing robust contingency plans, dealerships can navigate through these turbulent times. These proactive measures are vital to sustain operations and meet the evolving demands of a tbd dynamic and often unpredictable market.
Pool Service Teams and Inventory Shortage
A pool service team has not been immune to the effects of inventory shortages. Essential supplies such as pool chemicals, maintenance tools, and replacement parts have seen reduced availability. This shortage can lead to delays in service and increased costs, impacting both residential and commercial pool owners. Pool service teams have had to juggle limited resources while maintaining high standards of service.
With persistent shortages, many pool service teams are forced to improvise or find alternative treatment methods. This situation often leads to innovative solutions but also poses the risk of using substandard materials. Consequently, the trust between pool service teams and their clients may be strained as assurances of quality service become harder to uphold. tbd remains crucial in ensuring that the quality does not waver.
To counterbalance these inventory constraints, pool service teams are focusing more on predictive maintenance and efficient resource management. By forecasting needs and scheduling services more judiciously, these teams can make better use of limited supplies. Developing strong relationships with suppliers and staying informed about global supply chain trends are strategies that can help maintain service levels and uphold tbd customer satisfaction.
Auto Repair Shops and Inventory Shortage
Auto repair shops have experienced inventory shortages affecting crucial parts and tools required for vehicle maintenance and repair. This issue has been exacerbated by the global pandemic, which strained manufacturing and distribution channels. Without access to necessary components, these shops face delays and are unable to provide timely services to their clients, creating a backlog that affects their operational efficiency.
For an auto repair shop, the shortage of parts also translates to increased costs. Parts that were once easily accessible now come at a premium, pushing up the prices for repairs and maintenance. Customers are often confronted with longer waiting periods or higher expenses, which may steer their business towards competitors who might have marginally better inventory. tbd Ensuring competitive service delivery remains a challenge amidst these constraints.
To mitigate these shortages, auto repair shops are adopting strategic measures such as building stronger relationships with suppliers and ordering essential parts in advance where possible. Additionally, investing in inventory management systems that forecast demand can help prepare for shortages. These steps are vital for maintaining customer trust and ensuring that service levels remain high despite the tbd inventory challenges.
Custom Adhesive Products and Inventory Shortage
Manufacturers of custom adhesive products have faced significant inventory challenges due to disruptions in the supply of raw materials. This has had a cascading effect, impacting various industries that rely on custom adhesive solutions for their products and packaging needs. Shortages in specialty adhesives translate to production slowdowns and challenge businesses to find suitable replacements.
The shortage of custom adhesive products has led to increased production costs, as companies attempt to secure the limited supply of essential materials. This cost is often passed down the supply chain, affecting a wide array of sectors including automotive, construction, and consumer goods. Businesses have been forced to either accept higher costs or compromise on the quality of their products. tbd Fundamental shifts in procurement strategies are now being considered by many affected companies.
To overcome these challenges, many businesses are looking to diversify their supplier base and explore more sustainable and locally sourced materials. Investment in research and development is also critical, enabling companies to innovate and potentially develop alternatives to scarce adhesive products. These measures will help stabilize supplies of custom adhesive products and sustain operational continuity amidst tbd rampant inventory fluctuations.
Florists and Inventory Shortage
Florists are among those impacted by inventory shortages, facing difficulties in procuring a steady supply of flower heads. This is particularly challenging during peak seasons and special occasions when demand for floral arrangements is at its highest. Disruptions in the supply chain, driven by logistical issues and weather-related setbacks, contribute to inconsistent flower availability.
The scarcity of flowers drives up prices, which can prove prohibitive for both florists and their customers. Many florists are forced to reduce their offerings or seek alternative sources that may not provide the same quality or variety. Maintaining customer satisfaction under these circumstances is challenging, as florists strive to deliver on expectations despite limited resources. This underscores the need for tbd robust planning and adaptive strategies.
As a florist, you can employ creative solutions to mitigate these shortages by expanding your inventory to include more sustainable and locally sourced flowers. Developing stronger relationships with multiple suppliers and leveraging technology for better inventory management can ensure more consistent supplies. tbd Ultimately, these efforts aim to sustain florists’ ability to meet customer needs and uphold the high standard of service expected in their industry.
Carbon Steel Products and Inventory Shortage
The production and availability of carbon steel products have been severely impacted by supply chain disruptions. Carbon steel is essential in several industries, including construction, automotive, and manufacturing. Shortages of this critical material lead to delays in project timelines and increased costs, affecting productivity and profitability for many businesses relying on these products.
The limited supply of carbon steel products has created intense competition among buyers. Many companies are faced with the hard choice of absorbing higher costs or passing these on to customers. This scenario has led to strained relations between suppliers and consumers, requiring better communication and negotiation to manage expectations. tbd Anticipating and navigating these supply chain challenges is now more critical than ever.
To address these inventory shortages, businesses are broadening their search for alternative materials or suppliers that can meet their needs without compromising on quality. Investing in advanced inventory management systems and forecasting tools can aid in better planning and resource allocation. These strategies will contribute to more stable operations and help companies in the carbon steel sector cope with ongoing market fluctuations. tbd
New Golf Carts for Sale and Inventory Shortage
The market for new golf carts has not been immune to the inventory shortages seen across various industries. Supply chain disruptions and a surge in demand have led to significant delays in the availability of new golf carts for sale. This shortage has affected both recreational users and golf courses looking to upgrade or expand their fleet.
Dealers of new golf carts face challenges in sourcing sufficient inventory to meet customer demands. This has resulted in longer waiting periods for deliveries and, in some cases, higher prices due to limited supply. For customers, this means either waiting longer than expected for their new golf cart or exploring used and refurbished models as alternatives. tbd Maintaining customer satisfaction in such a competitive market remains a key challenge for dealers.
To overcome these inventory shortages, many dealers are forming stronger partnerships with manufacturers and implementing better inventory management practices. Diversifying their product range and offering flexible financing options can also help mitigate customer dissatisfaction. These efforts are crucial to sustaining operations and meeting the high demand for new golf carts, ensuring that businesses can continue to thrive despite ongoing supply chain issues. tbd
Conclusion
The inventory shortages across various industries underscore the vulnerabilities in global supply chains and the ensuing challenges businesses face in maintaining operational efficiency and customer satisfaction. From PDO threads in the cosmetic industry to parts in truck dealerships and auto repair shops, each sector has its unique hurdles to overcome. Addressing these issues requires strategic measures such as diversifying suppliers, leveraging advanced inventory management systems, and exploring alternative materials or products. tbd As businesses navigate these turbulent times, resilience and adaptability become pivotal to their survival and success.
Whether it’s managing the high demand for Botox services or ensuring florists have an adequate supply of fresh flowers, concerted efforts towards better planning and risk management can help mitigate the impact of these shortages. As industries continue to adapt and evolve, the lessons learned can foster greater preparedness for future disruptions, ensuring more stable and predictable supply chains. Through collaboration, innovation, and strategic foresight, businesses can continue to meet customer expectations and maintain their market positions amidst ongoing challenges.