Inside the Industrial Steel Tube Manufacturing Process From Coil to Fittings
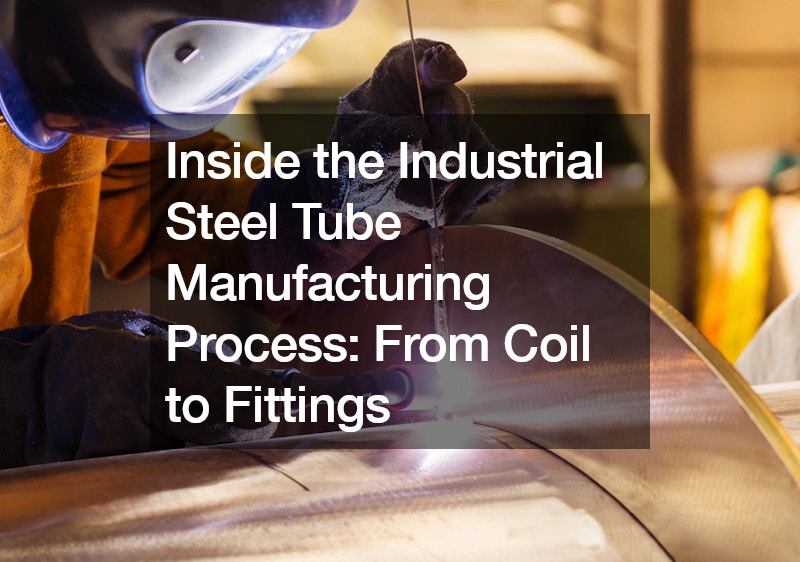
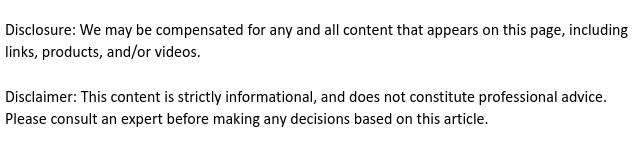
Industrial steel tubes are the backbone of countless applications, from construction and infrastructure to machinery and energy production. Their strength, durability, and versatility make them a crucial material for projects of all sizes. But how are these seemingly simple tubes actually made? This comprehensive guide delves into the fascinating world of industrial steel tube manufacturing, tracing the journey of raw steel from coil to finished product, including the creation of industrial pipe fittings that connect these tubes to form complex piping systems.
Understanding the Steel Tube Landscape:
Industrial steel tubes come in various shapes, sizes, and wall thicknesses. The two main categories are:
Seamless Steel Tubes: These tubes are formed from a solid steel billet, pierced, and elongated to create a hollow structure without any welds. Welded Steel Tubes: Formed from steel coils or sheets, welded steel tubes involve joining the edges using various welding techniques like electric resistance welding (ERW) or submerged arc welding (SAW).
The Journey Begins: Raw Material Preparation
The manufacturing process starts with high-quality steel. Here’s a breakdown of the initial steps:
Steel Selection: Manufacturers choose steel grades based on the desired properties of the finished tubes, considering factors like strength, corrosion resistance, and weldability. Surface Inspection: The steel coils or billets undergo rigorous inspections to ensure they are free of surface defects that could compromise the final product’s integrity. Preparation and Cleaning: The steel is cleaned to remove any contaminants like oil, rust, or mill scale that could affect the welding process or final product quality. Shaping the Steel: Manufacturing Techniques
Depending on the desired tube type, seamless or welded, different manufacturing techniques are employed:
Seamless Steel Tube Manufacturing:
Piercing: A hot solid steel billet is pierced using a piercing mandrel to create a hollow shell. Rolling: The pierced shell is then passed through a series of rollers, progressively reducing its diameter and wall thickness while elongating its length. Sizing and Straightening: The rolled tube undergoes sizing processes to achieve the precise dimensions and is straightened to ensure a uniform shape. Heat Treatment (optional): In some cases, the tubes undergo heat treatment to enhance their mechanical properties like strength and ductility. Finishing: The final step involves cutting the tubes to desired lengths, conducting final inspections, and applying any necessary coatings for corrosion protection. Welded Steel Tube Manufacturing:
Coil Slitting: Steel coils are cut into strips of the desired width for the tube wall. Edge Forming: The edges of the steel strip are formed into a specific profile depending on the welding technique used. Welding: The formed edges are joined using various welding methods like ERW or SAW, creating a continuous seam. Sizing and Finishing: Similar to seamless tubes, the welded tubes undergo sizing, straightening, cutting, inspection, and optional coating processes. Quality Control Throughout the Process:
Maintaining consistent quality is paramount. Here’s how manufacturers ensure their tubes meet industry standards:
Non-Destructive Testing (NDT): NDT techniques like ultrasonic testing and eddy current testing are employed to detect any internal cracks, voids, or other defects in the finished tubes. Dimensional Inspection: Precise measurements are taken to ensure the tubes meet the specified diameters, wall thicknesses, and lengths. Hydrostatic Testing (optional): In some cases, tubes undergo pressure testing with water to verify their strength and identify any leaks. Beyond the Basics: Value-Added Services
Many manufacturers offer additional services to cater to specific client needs:
Cutting and Beveling: Tubes can be cut to precise lengths and their ends beveled for easier welding or connection to fittings. Threading: Internal or external threads can be applied to facilitate connections with various fittings and other components. Painting and Coating: A variety of coatings can be applied to enhance corrosion resistance, improve aesthetics, or provide specific properties like electrical insulation. The Final Chapter: From Finished Product to Application
Once all quality checks are complete, the finished steel tubes are packaged and shipped to distributors or directly to end users. These industrial workhorses find application in a wide range of sectors:
Construction: Structural tubes for buildings, bridges, and other infrastructure projects. Manufacturing: Machinery components, pipelines, and pressure vessels. Energy: Pipelines for oil, gas, and water transportation. Automotive: Frame components and exhaust systems. Agriculture: Irrigation systems and fencing materials. Conclusion: The Strength Behind Countless Industries
Industrial steel tube manufacturing is a complex yet fascinating process. From meticulous raw material selection to rigorous quality control, each step ensures the finished product possesses the strength, durability, and reliability demanded by countless industries. Understanding this process not only offers a glimpse into the world of industrial manufacturing but also highlights the vital role these seemingly simple tubes play in shaping our infrastructure, powering our industries, and facilitating our everyday lives.
The Future of Steel Tube Manufacturing
The future of steel tube manufacturing is one of continuous innovation. Here are some trends shaping the industry:
Automation and Robotics: Increased automation and robotics will likely streamline production processes, improve efficiency, and enhance worker safety. Advanced Materials: Research is ongoing to develop new steel alloys with improved properties like lighter weight, higher strength, and enhanced corrosion resistance. Sustainable Practices: Manufacturers are increasingly focusing on implementing sustainable practices throughout the production chain, minimizing environmental impact and resource consumption. A Foundation for Success: Choosing the Right Steel Tube Supplier
For businesses that rely on industrial steel tubes in their operations, selecting the right supplier is crucial. Here are some factors to consider:
Product Quality and Reputation: Choose a supplier with a proven track record of delivering high-quality tubes that meet industry standards. Product Variety: Ensure the supplier offers a variety of tube sizes, shapes, wall thicknesses, and material grades to meet your specific project requirements. Value-Added Services: Look for suppliers who offer additional services like cutting, threading, coating, or even custom fabrication to streamline your procurement process. Customer Service and Support: Reliable customer service and technical support are essential for addressing any questions or concerns that may arise during the ordering or delivery process. By understanding the complexities of industrial steel tube manufacturing, staying informed about industry trends, and carefully selecting a reputable supplier, businesses can ensure they have access to the right steel tubes to support their operations, build lasting infrastructure, and propel their success.
.