How to Burnish Copper, Aluminium, Steel and Other Metals Using Roller Burnishing Method
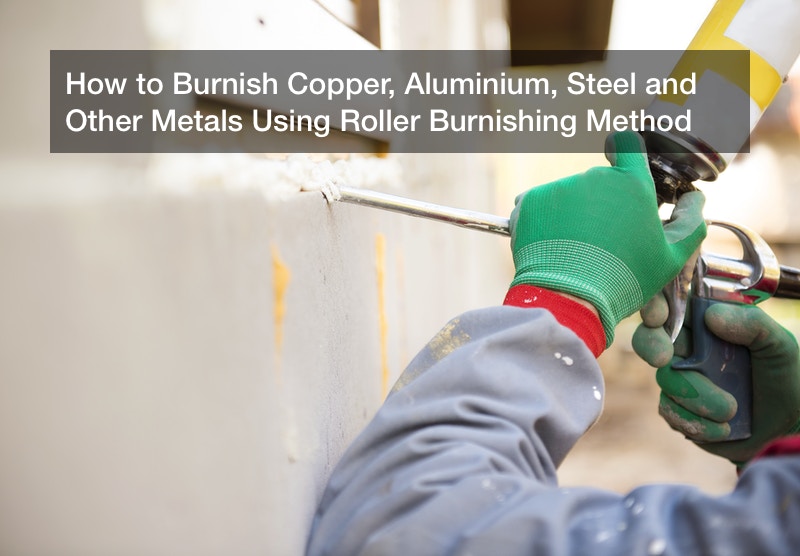
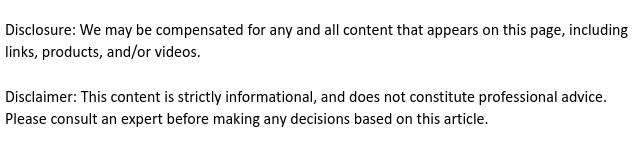
Sheet metals are crucial materials in the building, assembling, and construction industry. They are useful in sheet metal work such as automobile body building, fabrication, and structural engineering. Compared to standard metals, sheet metals are formed through an industrial process that thins and flattens them. Sheet metals can be bent and cut into various shapes and sizes. These metals can be fabricated from such metals as brass, copper, titanium, steel, and aluminum.
With the relevance and increasing need for sheet metals, finding the right place to buy them can prove a challenge. You might be wondering, how much is a piece of sheet metal? Seeking the help of an expert in finding places to buy metal will ease your mind. Working with an expert reduces the chances of being disappointed, especially when you have little or no experience. It is paramount to find precision sheet metal shops as these guarantee options depending on the metal type you are looking for. You also have the chance to see prototype fabrication, ask questions, seek clarification, and bargain for the best prices when you visit such shops. Check through the ratings when looking for precision sheet metal shops and create a list you can work with.
When it comes to precision metal finishing in order to achieve a mirror-like surface without subjecting the metal surface to more abrasive machining techniques such as grinding, even machining experts have a hard time determining which is the best method. There are various burnishing tools that can be used to achieve the perfect surface. However, the outcomes of the metallic surface are different depending on the tool used. This is the reason why you need to use the right burnishing method for the metallic surface depending on the desired outcome. If you do not wish to remove any metal from the part being burnished, then roller burnishing is the best solution for the perfect finish. Ideally, burnishing is the method of polishing metal by subjecting the surface to a harder surface. This is aimed at achieving a mirror-like surface for the metal surface. In order to understand how to use a burnishing tool, this method is a chipless machining method where there is no abrading or cutting of the metal surface. Instead of removing the surface, roller burnishing compresses the surface or rather irons out the peak of the metallic surface to generate a more uniform and dense surface. This improves the overall dimensional accuracy of the metal.
Different Approaches to Finer Roughness Values
During roller burnishing, there are two kinds of deformations that take place at the metal surface. The metal surface can either be subjected to either elastic deformation or plastic deformation. Elastic deformation occurs when the metal being burnished is subjected to stress that is relatively lower than the metal’s yield point. On the other hand, the surface can be described as being subjected to plastic deformation when the level of stress is higher than the material’s yield point. For example, crushing aluminum components such as aluminum can is plastic deformation since the material acquires a totally different shape and cannot be restored back to its original state. To put the definition of roller burnishing into perspective, think about when you squeeze a dimpled container from either side so as to push the dimples out. This is ideally what happens during roller burnishing. There is a common misconception with regards to what happens when a burnished surface is subjected to the roller during the process. Burnished surfaces not only acquire a smoother surface but are also hardened for better machining.
Which Parts Work for Roller Burnishing?
One of the things that makes roller burnishing a popular precision metal finishing is because it is fast and repetitive. You can achieve the desired metal surface in just a few seconds meaning that if you are involved in large scale need for burnished surface, then this is the best method chipless machining method. There is also the availability of tools that will enable you to have the right size, work-hardened and perfect finish in a matter of seconds. This is one of the benefits of using the roller burnishing methods over other machining methods such as honing, lapping and grinding. During the preparation parts of the process, you need to understand that not all surfaces are ideal for burnishing. There are a number of factors you need to take into consideration before commencing the process. One of the things you should consider is the material used. Although almost any metal can be burnished using the roller method, the best method for this method are those that have a high ductility or malleability. Such metals include stainless steel, aluminum components, brass, cast iron, alloys and bronze. You should also consider the hardness of the metal. The best metals for this method are those with a hardness of less than 40 HRC. This however does not entirely mean that metals with a hardness of more than 45 HRC cannot be roller burnished. The uniformity of the material used is also important since the outcome of the burnished surface will depend on the uniformity of the surface as well as wear and tear of the surface. Lastly, you also need to consider the roughness of the metal surface. In terms of roughness, the best surfaces for roller burnishing are those that are between 80- to 120-microinch.
Metal fabrics have different sizes, shapes, designs, and colors. They have an impact on the environment as about sixty percent of them are recycled. There are many types which include, rigid fabric, and helix and cable fabrics.
Commercial metal fabrication service
A commercial metal fabrication service does involve the creation of machines and structures from different raw materials. Fabrication costs between, $754 to $624 which cost both the materials and labor. The services are widespread across the country in form of blacksmiths and welding. The common materials used are stainless steel and aluminum.
Aluminum roofing manufacturers
There are many manufactures of aluminum roofing. This because aluminum light and hence easy to install. The cost of aluminum range, $9545 to $43819 depending on to the manufactures. Aluminum lasts between 40-70 years. The manufactures include Thomas net and China.
The Best place to buy sheet metal
Finding the best places to buy sheet metals is easy as one can go to different websites and ask friends. The best material is iron because it is cheaper than steel and lastly aluminum. Buying abroad is expensive as the shipping costs are high. Hence, advisable to find local industries.
Flat metal sheets for sale
Sheet metal is advantageous to others in that it is less expensive during processing and material cost. Different companies sell metal sheets. The prices tend change with quality and durability. There are also after-sale services like transportation and installation.
Hobby metals suppliers
Hobby metal suppliers are the best and the largest stores in Canada. The materials they offer include aluminum tubes, brass tubes, stainless steel, and sheet metal. They also offer after-sale services like installation and repairs.
Related Topics:
roller burnishing tool price, agate burnishers jewelry, ball burnishing tool, burnished steel finish, burnishing adapter, burnishing attachment, burnishing equipment, burnishing process, burnishing tool for lathe, how to burnish, how to burnish cast iron, how to make a burnishing tool, id burnishing tool, metal burnishing machine, plastic burnishing tool, roller burnishing process, what is a burnished finish, barnishing, burnishing brush, burnishing technique, cogsdill roller burnishing tool.