The Right Wholesale Parts for the Factory
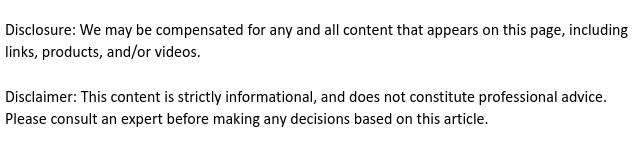
Today, the manufacturing industry is easily one of the largest in the United States, and it employs many millions of Americans across many different companies, large and small alike. In fact, even if it stood on its own, the American manufacturing industry would rank among the top economies in the world, and it may grow even more in the coming years. But every factory or workshop owner must remember the basics to keep these facilities running, and that means working with tool supply companies. These wholesale companies can be found online and by phone, and they can provide drill equipment such as ER20 collets, drill bit organizers and cabinets, drill chuck sleeves of all sizes, and more. With the right ER20 collets to clamp on a tool bit, for example, a good day’s work can be done in any workshop. And that’s not all. Carbide grinders and machine lube should be ordered, too. When is it time for new ER20 collets or grinder parts?
Drills
ER20 collets, diamond drill bits, chuck sleeves, and more are needed to run and operate handheld drills at a factory. Drills of all types are cutting tools designed to remove material in order to create desired holes, typically with circular cross-section work. Drilling is one of the major forms of machining, along with sawing and welding, and drilling can put holes in metal or wood to allow air, wires, screws, and more to pass right through as intended. Drills are nearly always power tools, since metals are too tough for hand-operated drills of centuries gone by to work on.
Drills are very common, and they can be used for machining just about anything from computer parts to household electronics to car parts and more. In fact, some 84% of contractors say that their most commonly used cordless power tool is a power drill in particular. A drill’s teeth allow it to remove material from the machined object and discard it, and scraps of metal or wood may be ejected from the work site to create a clean hole. But it may be noted that drills, for all their power, will create some rough imperfections on the machined material afterwards, and this is where carbide grinders come in.
Carbide Grinders and Lathes
Machining a piece of metal or wood will create burrs, or upraised imperfections of material. These rough burrs are a problem, since at the very least they look ugly on the finished project, and at worst they may scrape or scratch other surfaces during work or they may even attract static electricity. After something has been drilled, sawed, or welded, the item will be placed on a lathe table and held in place with an assembly. Now, the item is slowly fed to a grinder surface, and rotating grinder surfaces may have their RPM adjusted for different jobs. These surfaces simply grind off the burrs as they are fed, and this results in a smooth surface. All workshops and factories make use of these grinders to create smooth surfaces in objects. Meanwhile, burnishing tools can be used to compress, smooth out, and toughen metal surfaces.
The Right Lube
Well-oiled machines may be taken for granted, but a factory or workshop owner shouldn’t take machine lube lightly. These supplies must always be ordered in the correct type and amount from wholesalers, since the right lube will keep machines running for much longer. Lubes serve multiple functions, chief among them making sure all surfaces can easily glide and slip past each other without undue friction. These lubes may also prevent surfaces from getting dangerously hot, and they can even prevent static electricity buildup or prevent rust formation. Any startup factory or workshop must order the right lubes for all machines before operation, and local wholesalers can be contacted for that need.
Many factory owners admit that not all of their machines are properly lubricated, and many accidental factory shutdowns today are due to improperly lubricated machines. Some factory owners also admit that their staff are not fully trained on applying lube to machines, but any factory owner can take the steps to launch a more rigorous training program for lube use. This can prevent expensive machine shutdown due to worn out or overheated machines that were not lubricated.