The Three Methods of Plastic Blow Molding
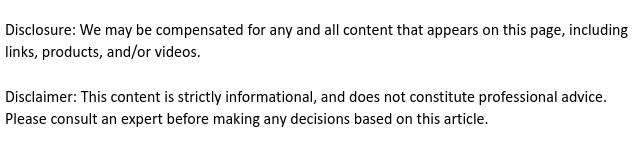

The custom bottle manufacturing industry is blowing up. People like custom bottles not only to use and and have practical need for but also to collect and simply have around just in case. There are three different ways that various kinds of colored bottles and blow molded containers are made. They are knows as extrusion, injection and stretch blow molding cases. Bottle companies use one or all of the methods in order to make plastic handleware, bottles and jars. Custom bottle manufacturing utilize these three methods as well. Let’s look a little deeper at each one.
General Information Regarding Blow Molding
THe first thing that you should is that blow molding is the process of manufacturing when a hollow plastic part or parts are made. The whole process starts by melting down a piece of plastic in order to make it into a parison or a preform, depending on the method that you are using. The parison or preform is later put into a mold to have air blown through it. The air pressure is used to push the plastic until it matches the sides of the mold. Once the plastic cools down, it will harden and the mold can be opened and the piece removed.
Extrusion Blow Molding
Extrusion molding in particular is part of the custom bottle manufacturing process that involves the plastic being melted and then captured in a metal mold that has already been cooled. The rest of the process is pretty much the same. The cooled metal mold will hold the plastic melted pieces so that the air can flow into the part, pushing it against the sides of the mold. When the melted plastic is pushed against the cold metal, it will set more easily and quickly because of the cold encounter.
Injection Blow Molding
This is the custom bottle manufacturing process for extremely high quality bottles that have a high clarity quality. Once the plastic is melted and put in the mold, it forms a preform rather that a parison. This is usually pre heated and then injected into the mold between the two halves. The injection molding can be done with various materials, not just plastic. Metal, glass, elastomers, confections and other things like thermoplastic and polymers are also commonly used in this method.
Stretch Blow Molding
This is probably the most common way that plastic bottles are made. In fact, almost all soda bottles are made like this. The two methods involved in stretch blowing is single stage and two stage processes. The two stage process can create very high volumes of bottles. This process is what is usually used to soda bottles. The bottle designs can be varied; cylinders, rectangles, ovals and more. However, the capital cost is very high for this method. Also, there is a lot of floor space that is needed because the systems are not very compact.
The single stage process is more suitable for lower volumes of manufacturing and short runs. This is because the preform can not be released during the process. This means that the wall thickness will be an even thickness. However, you will be limited when it comes to bottle design for this method. It is only possible to make what is known as a champagne base when you are making bottles for carbonated drinks.
As with everything, there are pros and cons to each method, depending on what you are trying to make and in what volume. However, they all come down to melting plastic and reforming it in to the shape that you want it to be.
It’s been long since thought that plastic is bad for the environment but the great thing about some of these methods is that they can take already used plastic and melt down again to reuse it. Who would have thought that they would be recycling, reducing and reusing when it came to plastic? But technology has come far enough in this day and age, that recycling plastic bottles and materials is one of the main ways that you can help the environment and save the planet. As long as we continue to melt and reform plastic, it is not so bad to drink out of plastic bottles.