All You Need to Know About Blister Packaging
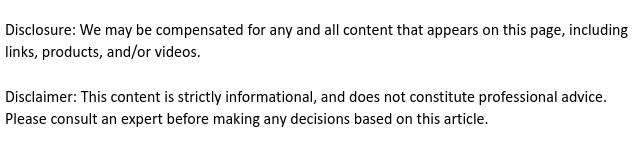

We have all been there, trying to open our prescription medication and struggling so hard to open it. Either you have a tricky blister pack to get through, or a simple bubble to pop, medical packaging materials can be pretty complex. Here is all you need to know about medical blister packaging.
What is blister packaging?
The term blister pack is used to describe pre-formed packaging that is meant to protect anything from food to small consumer goods to pharmaceuticals. Usually, they consist of thermoformed plastic that has a backing of cardboard, aluminum foil, or plastic. These layers are primarily designed to protect the contents from outside factors like humidity, contamination from debris, and to shield light from light-sensitive medications.
What are their uses?
It differs per what product they are protecting. For consumer goods, they are used to showcase the product through clear plastic so the consumer can examine what they are buying. This plastic shell is vacuum sealed to form a snug fit around the product, but is not too tight where the buyer cannot open it.
For pharmaceutical medicines, the most popular type of a blister pack is for unit dosages. A popular example of this is women’s birth control, where each pill is separated per day it needs to be administered. Another example is cold medicine that must be administered every 12 hours or so, the patient will get a package and must individually open each pill. One can also notice blister packs on medical samples given out by physicians in order to prevent tamper resistance.
How are they produced?
Blister packs are produced by using two methods, thermoforming and cool forming. Pharmaceutical packaging companies choose their preferred method, but they may utilize both.
Thermoforming is when a plastic film or sheet is unwound from the wheel, heated, and when pliable it will be put into a mold. Cold forming is when a sheet of aluminium foil is placed onto the packaging like a stamp to create a barrier preventing oxygen and water from getting into the medication. But the cold forming process is a lot slower than thermoforming, and is not as flexible to different shaped packs.