Tips to Boost Efficiency in Prototyping and Rapid Manufacturing
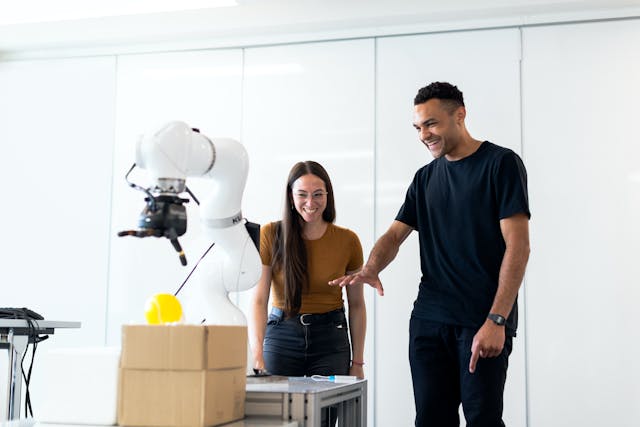
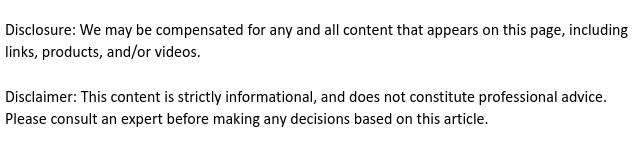
- Utilize 3D printing to rapidly produce prototypes, allowing for quicker iterations and enhanced design flexibility.
- Strengthen collaborations with suppliers to ensure material availability and gain insights into cost-saving and efficiency measures.
- Invest in automation to speed up production, reduce errors, and free up the workforce for strategic tasks.
- Implement lean manufacturing principles, including JIT and 5S methodology, to minimize waste and optimize processes.
In today’s fast-paced business world, efficiency is critical to staying ahead of the competition. When it comes to prototyping and rapid manufacturing, every minute counts. Here are essential tips to help you boost efficiency in your prototyping and manufacturing processes. These tips will help you streamline your operations and get products to market faster.
Utilize 3D Printing Technology
One of the most effective ways to boost efficiency in prototyping and rapid manufacturing is by using 3D printing technology. With 3D printing, you can quickly produce prototypes and small batches of products without the need for expensive tooling or long lead times.
This technology allows for rapid iteration and testing, helping you bring products to market faster. 3D printing also allows for customization and design flexibility, giving you the ability to create unique products that stand out in the market.
Collaborate with Suppliers
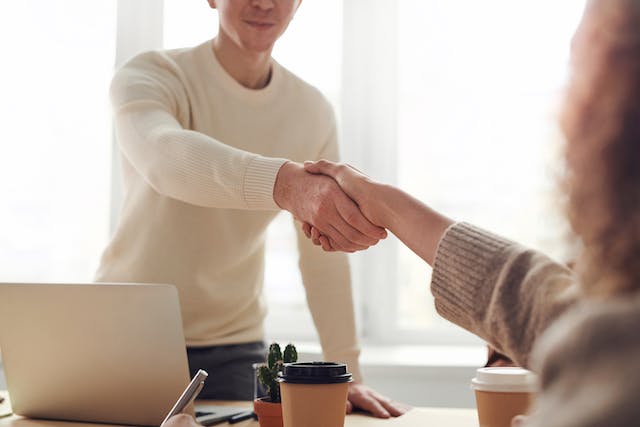
Building solid relationships with suppliers can also significantly improve efficiency in prototyping and manufacturing. By working closely with your suppliers, you can ensure that materials are readily available when needed and that production runs smoothly. Additionally, suppliers may be able to provide valuable insights into cost-saving measures or alternative materials that could streamline your processes.
Invest in Automation
Automation technologies such as robotics or automated assembly lines can significantly enhance efficiency in prototyping and rapid manufacturing. By automating repetitive tasks, you can free up your workforce to focus on more strategic activities while increasing production speeds and reducing errors. While automation may require an initial investment, the long-term benefits in terms of increased productivity and cost savings make it a worthwhile investment.
Outsource Certain Processes
Outsourcing specific processes can also help streamline your prototyping and production processes. By leveraging the expertise of specialized service providers, you can reduce costs and lead times while maintaining high-quality standards. For example, partnering with a laser metal cutting service provider can help you quickly and accurately create complex metal components for your prototypes or production runs.
They may also have the expertise to suggest alternative materials or design modifications that can save costs and improve performance. Just make sure to establish clear communication and quality control processes to ensure the outsourced work meets your standards.
Implement Lean Manufacturing Principles
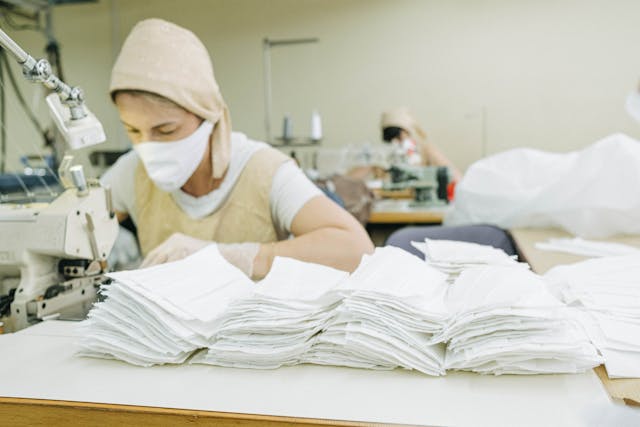
Adopting lean manufacturing principles can help eliminate waste and improve efficiency in your prototyping and manufacturing processes. Here are four fundamental principles to consider implementing:
Value Stream Mapping
Identify and map out the steps in your production process, then look for opportunities to eliminate unnecessary steps or streamline processes. You may find that specific steps can be combined or automated, leading to cost and time savings.
Just-In-Time (JIT) Production
JIT production focuses on producing only what is needed when it is required. This helps minimize inventory costs and reduces the risk of excess stock or waste due to design changes. You may also want to consider implementing a Kanban system, which uses visual signals to trigger production based on actual demand.
Continuous Improvement
Encourage ongoing evaluation and improvement of your processes by involving all team members in identifying potential areas for optimization. By constantly striving for improvement, you can reduce costs, improve quality, and increase efficiency.
5S Methodology
The 5S methodology is a system for organizing and maintaining a clean, efficient workspace. The five S’s stand for Sort, Set in Order, Shine, Standardize, and Sustain. Implementing this methodology can help reduce waste and increase productivity by creating a more organized and efficient work environment.
By implementing lean manufacturing principles, you can optimize your prototyping and manufacturing processes to minimize waste and increase efficiency. These principles can also help improve product quality and reduce costs, allowing you to stay competitive in the market. Additionally, by involving all team members in the continuous improvement process, you can foster a culture of innovation and collaboration within your organization.
The path to enhanced efficiency in prototyping and rapid manufacturing involves a blend of innovative technologies, strategic partnerships, and smart process management. By embracing 3D printing, collaborating with suppliers, investing in automation, outsourcing processes, and implementing lean principles, you can establish a more streamlined and cost-effective production process.
As technology continues to advance and new methodologies emerge, it is essential for companies to adapt and evolve in order to remain competitive in the fast-paced world of manufacturing. Constant evaluation and improvement are crucial to staying ahead of the curve and achieving success in prototyping and rapid manufacturing.