The Right Tools and Supplies for a Factory

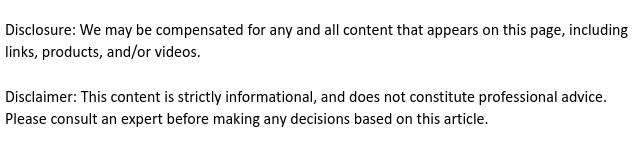
Your company has its minimum viable product (MVP) designed and a prototype perfected. It’s time to manufacture your product, but first, you’ll need to design your factory. Many factors go into designing your plant. Start by properly insulating your building.
According to the American Institute of Chemical Engineers (AIChE), all industrial operations use industrial insulation, but which insulation they use varies by industry. Like other types of insulation, industrial thermal insulation helps control the temperature. Building materials manufacturers make industrial insulators tougher, so they deftly handle extreme conditions and harsh environments.
These integral design differences mean you can’t use residential or commercial-grade insulation instead of an industrial insulator material. When hiring your general contractor to renovate the factory space you obtain, ensure they have ample factory design and renovation experience. Only through experience will a contractor know the subtle differences between the industrial-grade insulation needed for a small-scale wine-making operation and an ice cream manufacturing plant.
Rather than forging direct vendor partnerships with purveyors of industrial insulation supplies, work through your general contractor to purchase the materials needed. Read about design best practices that lead the way in your industry and ensure that the materials used on your project meet the same standards. Now, let’s consider some of the many other factory necessities, such as lathes, drill bores, and saws.
The American manufacturing sector is truly enormous. In fact, if it stood alone, it would be the world’s eighth largest economy, based on GDP. It contributes some $2.17 trillion to the American economy, and every $1 spent on manufacturing adds another $1.40 to the economy overall. Over 256,000 manufacturing firms large and small are in operation across the United States, and all manufacturers of all sizes need the right supplies and parts to keep running. So, factory owners and workshop staff can order drill bores of all sizes, burnishing tools, PCD tools, lathe tables, pressurized gas canisters, and even lubricants. But what is a burnishing tool used for, and what is there to know about using various drill bores on sheet metal? Assembling a piece of machinery requires many different steps.
Lathe Work and Drill Bores
The term “machining” describes the use of drill bores, saws, welding torches, and more to alter how a piece of metal, wood, or plastic is shaped. For example, drill bores can carve round holes into a piece of metal so that screws may be inserted later, or a laser cutter head carves thin lines into a piece of plastic. This is all and well, but take note that machining is somewhat sloppy work. When an item is drilled or cut, there will often be rough, upraised imperfections known as burrs, common on wood and especially metal. Such burrs are a problem, since they can scratch or scrape other surfaces when an item is used, or even attract static electricity. And if nothing else, such burrs are unsightly and will not impress merchandise buyers.
Modern tools can scour those burrs right off, before the product is finished, and that is the job for lathes. The very concept of lathes dates back to ancient Egypt, and today’s lathe tables are electric and operated with computers. In short, a piece of metal or wood is held in place with a lathe table’s assembly, and then it is slowly fed to a rotating grinder surface. That surface’s RPM can be adjusted according to need, and in any case, the grinder will simply scrape off any upraised burrs on the item and leave behind a smooth, flawless surface. This may be done on anything that was drilled, or anything that was cut with physical saws or welded.
Burnishing
Next, let us consider burnishing, an important step for making a metal item. Burnishing is when a sphere of metal is applied to a metal item with great pressure, and rolled around smoothly across the entire surface. Burnishing like this will compact a metal surface somewhat, and allow it to endure more pressure and weight. Burnishing can also smooth out the metal and make it look more attractive. Many metal products today are advertised for having burnished surfaces, something that any buyer would like. Even jewelry can be burnished, and products can be re-burnished to improve their appearance. Jewelry burnishing often involves placing all jewelry into a rotating drum that is filled with metal bits.
Gas and Lube
These supplies are quite important for the operation of machines in a factory or workshop. Some cutting or etching work is done with laser cutter heads, which emit very hot, highly concentrated beams of light that can slice through wood, metal, and plastic alike with great precision. This greatly reduces the incident rate of burrs, and allows for precise work. Laser cutter heads make use of not jut light, but also delicate lenses as well as pure, pressurized gas to operate. If that gas runs low or suffers contamination, the workers can order fresh new gas canisters and resupply their machines. Should the gas be faulty, the workers can order ultra-pure calibration gas and compare both gases to diagnose a problem.
Lubricant is vital for all moving machines, and proper lubrication can prevent machines from overheating, scraping and scratching one another, and more. Many factory shutdowns are attributed to machines that broke down or overheated due to improper lube application, and many factory owners admit that their workers are not entirely versed in the use of lubricants. But the diligent ordering and use of lube supplies, and fully training all employees, can help prevent those expensive breakdowns.