Why are Airplane Seats So Uncomfortable?
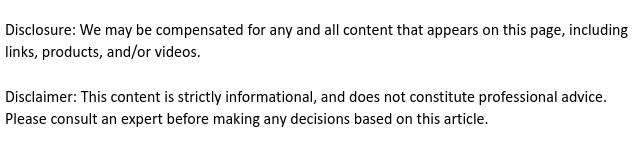

Commercial travel is the most popular way for Americans to traverse the world, although it may not be the most comfortable. A TripAdvisor poll found that comfortable seating is one of the most important factors for 30% of Americans. There is nothing worse than the cramped leg room, uncomfortable material, and lack of support for those who have had to endure extended flights.
The Wear and Tear of Flight
Airplane seating needs to be durable as they cannot easily be repaired or replaced. Since most planes make several trips per day and carry a combined average of 8 million people across the globe every day; because of this need for durability, comfort is often sacrificed as fabrics would typically be too weak at the seams due to stitching. Even the seat belts need to be tougher on an air plane as they can lose up to 6% of their strength with a single twist — continued twisting can cut the durability of a seat belt down by 40%. While it would seem that comfort is simply unattainable for those of us stuck in coach, in reality the fabrication industry has already developed a technique that can replace stitching to produce stronger bonds.
Sewing at the Molecular Level
While welding is typically used for metals, there are innovative processes that allow materials like vinyl-based fabrics, polyurethane, and PVC plastics to be welded together just as easily as metal welding allows. One such process, radio frequency welding (RF welding) uses high frequency electromagnetic waves to heat and weld materials that are held in place on a table using custom made dies. The vibrations of the radio waves actually heat the material, causing a strong and durable bond. Many industrial sewing companies that produce textiles for hospitals, airlines, and automobiles use RF welding fabrication to provide superior bonds that last longer than traditional stitching. Though it sounds modern, industrial sewing techniques like RF welding have been around since the 1940s continue to advance the industry even today.