Why Different Types of Steam Traps Are Used Throughout All Industries
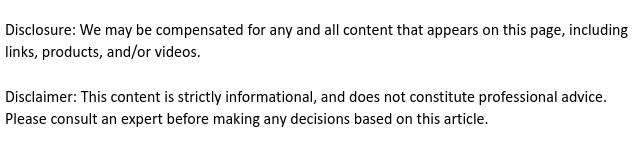

As industrial processes have expanded and evolved over the past century, people are constantly on the look out for sources of power that are more efficient and powerful than previous methods. At one point, almost everything was run from the burning of coal. We then moved on to the use of the combustion of fossil fuels into power through combustion engines. Currently we have settled on the most economical source of power to date, electricity.
While electricity itself can offer a lot of power, other techniques have been developed that harness electricity to facilitate other power generating processes. Different types of steam traps are mechanisms that use electricity to heat water inside of a container, transforming it into steam. The gas that is released is not only very hot, but when being pushed out through a valve, can have an enormous amount of pressure that can in turn be used to power other mechanisms.
The problem that comes along with using different types of steam traps, is how essential regular maintenance is. Like any other machine that stores or controls gases, all elements of steam trap parts must be sealed properly to get the best performance. Just using quality equipment and regular steam trap testing can reduce steam losses to less than 1%, which over time can save substantial amounts of money on operation costs.
It’s estimated that 20% of the steam that leaves the central boiler plate inside a trap is lost via leaking pieces in any typical space heating equipment. Much of this can easily be resolved through regular steam trap maintenance.
Fortunately, Standard Industry Steam Traps come with a one year warranty, but can typically last anywhere from three to seven years depending on the environment it is being used in, as well as how often it is serviced. With so many different types of steam traps in use throughout the manufacturing industry, ensuring that steam products are working at optimum efficiency facilitates countless operations in the every day lives of people.