Logistics Outsourcing: 4 Mistakes You Must Steer Clear Of
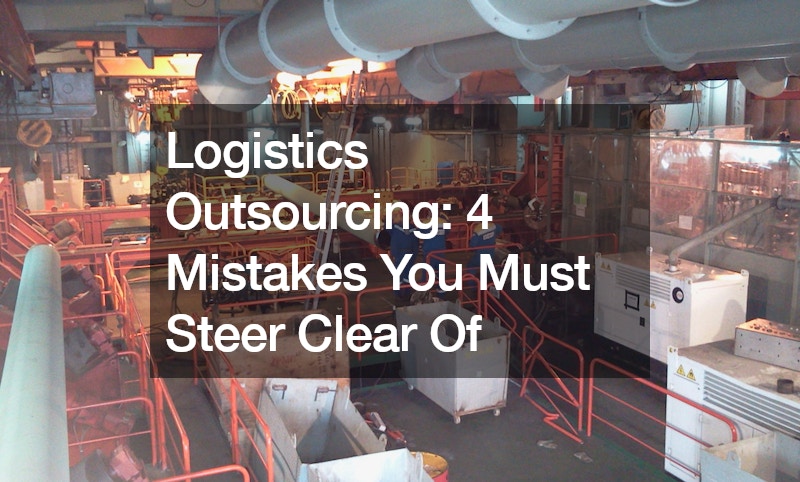
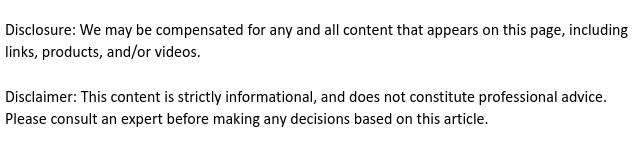
In this globalized business landscape, logistics outsourcing has become increasingly common. From warehousing to freight management, companies often seek third-party providers to streamline operations and reduce costs. Still, despite the benefits of outsourcing, many businesses stumble due to common mistakes that could have been avoided with proper planning and foresight. This blog post will delve into four critical errors that companies must steer clear of when outsourcing logistics.
1. Rushing the Time Frame
One of the most prevalent mistakes companies make when outsourcing logistics is rushing the time frame. In their eagerness to expedite the process and reap the benefits quickly, businesses often underestimate the time required for thorough planning, documentation, and evaluation.
From drafting detailed requests for tender to conducting site visits and negotiating contracts, each step demands adequate time and attention.
By rushing the time frame, companies risk overlooking crucial details and compromising the quality of the outsourcing arrangement. Insufficient time may lead to hastily prepared documentation, vague service level agreements, and incomplete evaluations of potential service providers. Ultimately, this haste can result in suboptimal contracts, escalating costs, and operational disruptions down the line.
To avoid this pitfall, businesses must approach logistics outsourcing with patience and diligence. Allocating ample time for each stage of the process ensures comprehensive planning, thorough evaluation, and informed decision-making. By prioritizing quality over expediency, companies can forge successful outsourcing partnerships that deliver long-term value and efficiency.
2. Neglecting Data Accuracy and Detail
Another common mistake in logistics outsourcing is neglecting data accuracy and detail. Effective outsourcing relies heavily on accurate and comprehensive data regarding product profiles, customer locations, transaction histories, and performance metrics. However, some companies fail to provide potential service providers with the necessary data, leading to inaccurate cost estimations and inadequate solutions.
Without access to detailed data, service providers may resort to making assumptions or relying on incomplete information, resulting in suboptimal solutions and cost overruns. Moreover, inaccurate data can lead to misaligned expectations and disputes between the outsourcing company and the service provider, undermining the effectiveness of the partnership.
To mitigate this risk, businesses must prioritize data accuracy and detail when outsourcing logistics. Conducting thorough data audits and analysis ensures that all relevant information is available to potential service providers, enabling them to develop tailored solutions aligned with the company’s needs and objectives.
3. Lack of Clarity in Service Requirements
Clarity in service requirements is paramount when outsourcing logistics, yet it’s a mistake many companies overlook. Failure to clearly define the scope of outsourced services, service levels, and performance expectations can lead to misunderstandings, discrepancies, and disputes between the outsourcing company and the service provider.
Without clear and explicit service requirements, service providers may struggle to meet expectations, resulting in service deficiencies, delays, or additional costs. Ambiguity in service requirements can also hinder effective communication and collaboration between the outsourcing company and the service provider, impeding the achievement of mutual goals.
To prevent this pitfall, businesses must invest time and effort in defining clear and comprehensive service requirements before engaging with potential service providers. Detailed service level agreements, performance metrics, and escalation procedures should be documented and communicated effectively to ensure alignment and accountability. Clarity and transparency in service requirements can help companies establish a solid foundation for successful outsourcing partnerships.
4. Inadequate Selection of Service Providers
Finally, inadequate selection of service providers is a common mistake that can derail logistics outsourcing initiatives. Some companies fail to conduct thorough research or vetting processes when selecting potential service providers, resulting in mismatches in expertise, capabilities, or cultural fit.
Choosing the wrong service provider can lead to inefficiencies, service disruptions, or even reputational damage for the outsourcing company. Additionally, engaging with unsuitable service providers can undermine trust, collaboration, and long-term success in the outsourcing partnership.
To avoid this pitfall, businesses must adopt a strategic and rigorous approach to choosing service providers for logistics outsourcing. This involves conducting comprehensive market research and evaluating potential providers based on relevant criteria like experience in managing 3PL warehouses, technological capabilities, and adherence to industry standards. Engaging in thorough due diligence processes ensures that the chosen 3PL partner aligns with the company’s specific warehouse management needs and long-term objectives. If companies prioritize compatibility, expertise, and alignment with business objectives, they can maintain strong outsourcing partnerships that consistently bring value and innovate.
Final Thoughts
Businesses seeking to reap the benefits of logistics outsourcing effectively must avoid these four common mistakes. By prioritizing careful planning, data accuracy, clarity in service requirements, and strategic selection of service providers, companies can pave the way for successful outsourcing partnerships that drive efficiency, agility, and competitiveness in the modern business environment.
.