The Modular Build Process
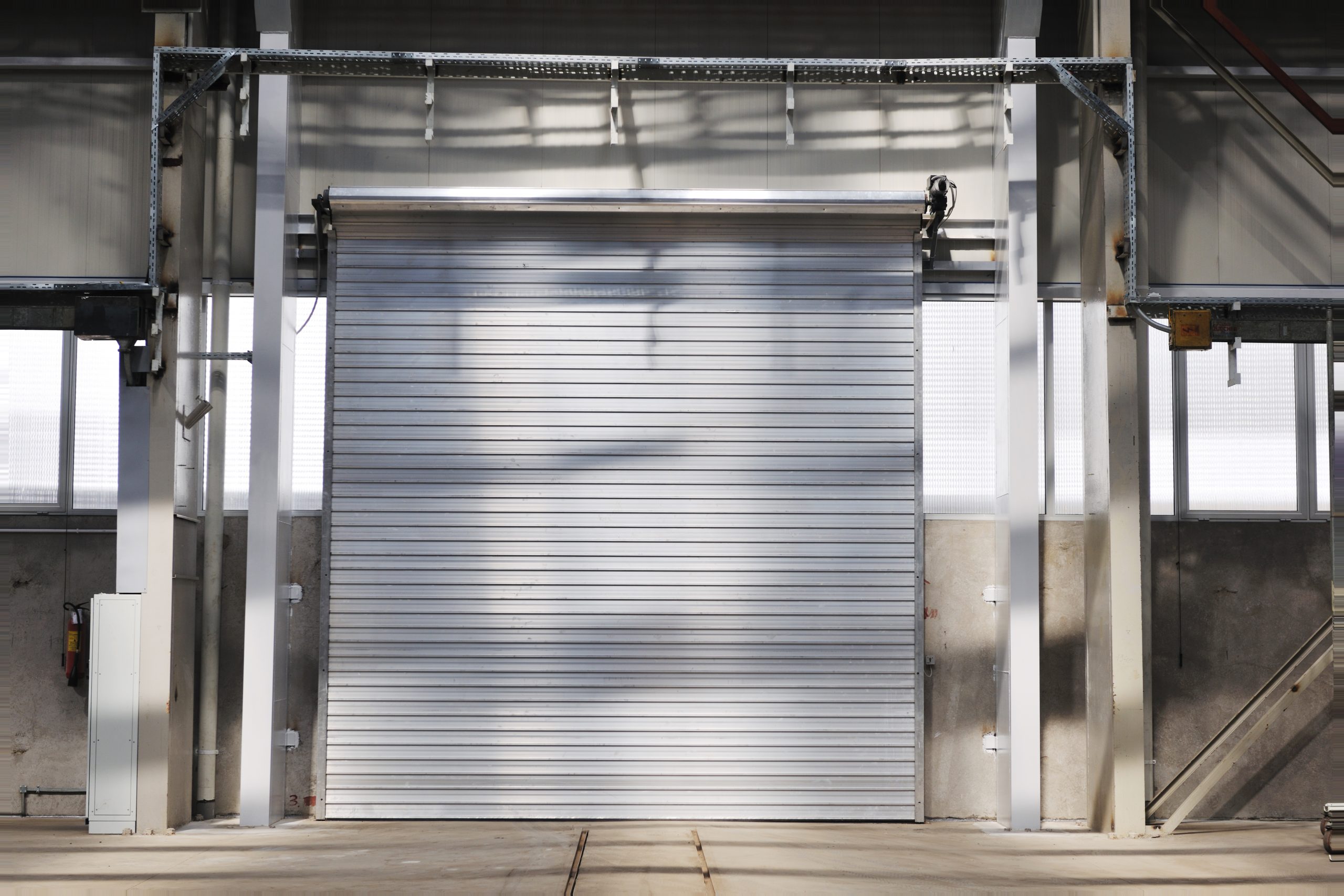
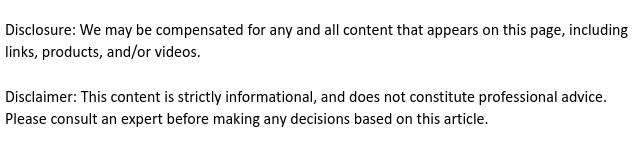
Modular warehouse offices are a great choice for the budget, space, the speed at which they can be built, and flexibility. In-plant modular offices are extremely popular because they make the most business sense.
Most people are at least aware of modular warehouse offices but are not aware of the process. If you are wondering how the modular building process work does, keep reading.
What Exactly Are Modular Warehouse Offices?
Many warehouses and plants have offices right on site. The offices typically house administrators and managerial staff. An in-plant office provides privacy without reducing accessibility for the employees.
In plant offices are either site-built (traditional construction) or they can be an in-plant modular office (and off-site-built structure that is installed on-site). Prefabricated offices have all their components built in a factory, then the components are put together on site.
Each part of the office is prefabricated in a controlled environment on an assembly line instead of building from the ground up at the location. You get tighter quality control when walls and other parts are prefabricated in a factory where there is an exacting method in place.
The First Steps
The modular build expert will consult with you to determine sizes, features, and finishes. Once measurements have been taken and style and design decisions are made, you are only weeks away from having your modular warehouse offices installed.
Framing, Walls, and More is Done Prior to Installation
Everything that you would expect an on-site construction build to do like framing is done on the assembly line. The difference is that in the factory the construction is closely monitored, there is a reduction of risk when it comes to errors. Of course, it also means less disruption in your warehouse. All the big work is done away from the site.
Each part is marked and ready to ship to the site quickly. On delivery day, everything arrives ready to be assembled. Waste is kept to a minimum as is the disruption to your employees.
It is a Time Savings and a Cost Savings
Modular construction can reduce energy consumption by about 67% which means it is a less expensive process. That saving is passed on to you. Modular offices can cost from 9% to 20% less than traditional construction costs.
The process from the factory floor to turnkey is also shorter than what you would find with traditional construction. Typically, the modular build process takes about 1/3rd of the time a site build project takes. This may exactly the solution you have been searching for. Learn more about the process and the costs today.