The Benefits of Using Modular Construction Techniques
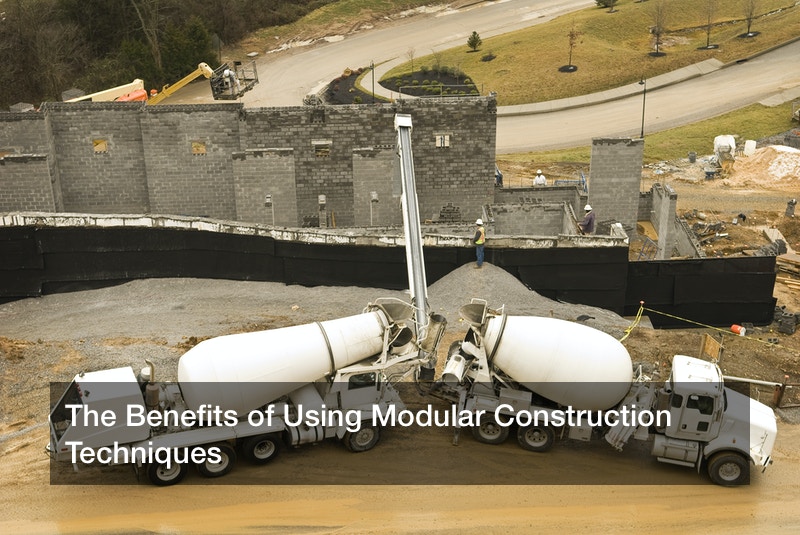
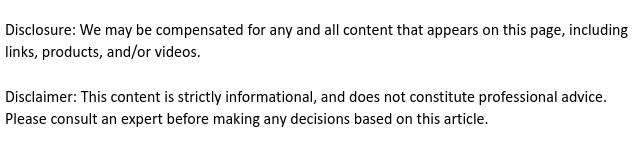
The American construction industry is truly enormous, and it has a market of over $1 trillion today. Construction companies work together to complete houses, schools, banks, libraries, office buildings, and more, but there is more than one way to complete a project like this. Traditional construction zones are still quite common, but now, modular office buildings are becoming standard as well, and an in-plant modular office can be built with remarkable resource efficiency. More and more often, American and foreign construction firms alike are opting for in plant office construction, and there is more than one good reason to build a room or office indoors like this. The same is true for warehouse offices and warehouse partitions, too. So, what goes into building in-plant modular offices, and what are the statistics to prove why this is a good idea?
Building Something Indoors
Constructing a building inside another building may sound odd at first, but this idea is perfectly viable if those new structures are being built one room at a time and then assembled in a modular fashion at the construction site, and that includes in-plant modular offices, among others. This idea is becoming popular fast: about 90% of engineers, 84% of contractors, and 76% of all architects are using prefab or modular construction methods for some or all of their projects. As of 2011, prefab and modular construction techniques were most popular for commercial applications such as healthcare facility construction (49%), dormitory and colleg4e building construction (42%), and manufacturing facilities 42%). In particular, Marriott International once pledged to use modular construction for 13% of all its North American projects in 2017.
There are many advantages to building in-plant modular offices and warehouse parts indoors like this. For one thing, the workers are under a roof, meaning that they (and the materials) are shielded from extremes of heat or cold, as well as snow, rain, and strong winds. Such construction can be done pretty quickly, too, compared to traditional methods. A Chinese modular construction firm was able to build a 57-story structure in just 19 days, for example. Modular construction also means slashing energy consumption; energy use for the building process can be lowered by as much as 67% in some cases.
Perhaps the biggest perk of building in-plant modular offices is resource efficiency. At a regular construction site, a lot of materials will end up as scrap, and the crews there have to hire junk removal services whose trucks haul away scrap or unused wood, bricks, and more. But this is not the case with modular construction, and a report from the Building Industry Association of Philadelphia said that modular methods can reduce construction costs by 9-20%, too. It is efficient work in many ways. Further, the UK-based WRAP (Waste and Resources Action Programme) reported that modular construction methods can reduce waste by up to 90%, for materials ranging from bricks and timber to concrete, cardboard, plaster board, and more. By now, many industries are quite conscious of how much pollution and waste material they are generating, and going modular can help with the overall “go green” initiative.
Finishing Construction
A modular room is not only convenient to build, but also convenient to put into place. Such a modular room (offices, bathrooms, break rooms, etc) will have its utilities in it too, such was water pipes and electric components, so those do not have to be installed at the construction site. Instead, the modular room is simply fitted into piece like a building block, and the utilities can connect to each other quickly and easily. A modular room is ready to go from the moment it is fitted into place.
Other prefabricated materials include portable office walls or prefabricated office walls, and warehouse materials, too. A warehouse needs non-permanent walls, storage boxes, and dividers to accommodate ever-shifting amounts and types of items, so prefab walls are ideal. In fact, prefab warehouse walls can come complete with windows and doors, to form temporary and moveable offices and storage rooms on demand. Similarly, a complete, modular office can be brought into the warehouse and set in the middle of the work zone, so the manager inside is conveniently close to the workers and materials.