Modular Rooms and Warehouse Partitions
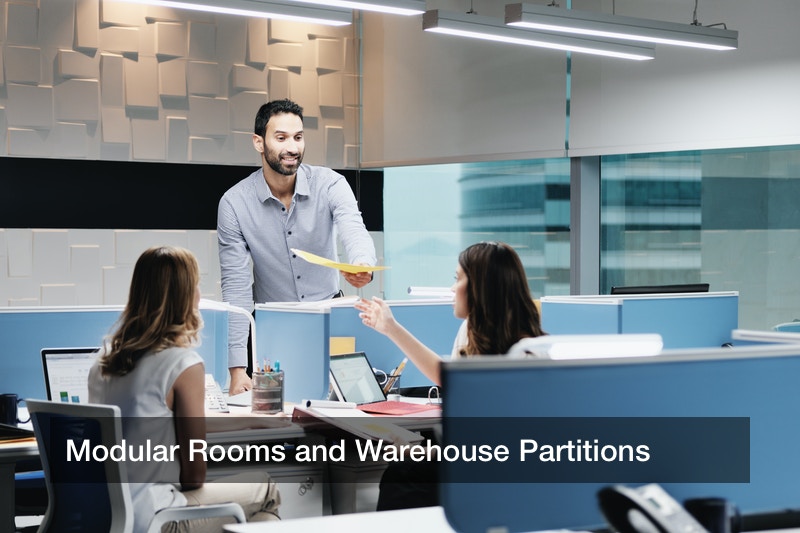
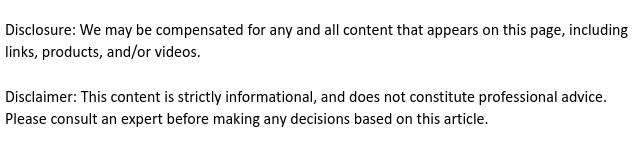
The modern construction industry is a truly vast one, and it is worth over $1 trillion today. Many construction firms big and small are hired to make offices, hotels, banks, schools, libraries, and more, but they are going to need the right materials and tools for the job. A new and strong option for this is in-plant modular office construction, and prefabricated office spaces and warehouse partitions offer a lot of advantages. More and more often, construction firms are using modular offices and warehouse partitions to finish a project, and warehouses in particular have acute need for portable offices and warehouse partitions. Warehouses need to adjust themselves for different stock and moving items, so non-permanent hardware is a must.
Modular Fabrication
What does it mean to build modular rooms or warehouse partitions, and what are the advantages of using this construction method? Put simply, a wall system or a room is built inside a factory or large workshop, from the bare bones right down to the fabricated walls, ceiling, and floor, not to mention utilities such as electricity in water. In short, the entire room is fully furnished and set up, and it is then transported to the construction site and fitted right into place. Once in place, the room is fully ready for use and occupancy, and it will have very few maintenance or finishing touch needs. All of that work is done beforehand, and buyers can order a custom-made modular room and ask for a quote. Such builders can handle a wide variety of jobs, and make rooms with different configurations and with different materials, as the customer needs.
This strategy for making modular rooms and warehouse partitions is becoming more and more popular, and over 90% of engineers, 84% of contractors, and 76% of architects are using these construction processes for at least some of their projects. As of 2011, prefab and modular construction was involved in making healthcare facilities, dorms and college buildings, and manufacturing facilities. Hotels in particular can use this technology, and Marriott once pledged to use modular construction for 13% of its North American developments in 2017.
Overall, using modular tech for warehouse partitions and modular offices reduces the cost and time needed to make a structure, and there are even some tax benefits to using this method. A major benefit of modular construction is the resource efficiency; as much as 90% of waste is eliminated, according to the UK-based WRAP (Waste and Resources Action Programme). Materials such as cement, bricks, wood pallets, timber, concrete, cardboard, and plasterboard can all be saved this way. By contrast, conventional construction sites often have to hire junk removal services to bring over huge trucks and haul away a lot of scrap and waste material, but using modular tech can eliminate that step entirely. Often, modular office factories can recycle and reclaim a lot of their spare and unused materials, so they are a major part of the overall “go green” initiative. Lastly, take note that modular construction can reduce energy consumption for the building process by 67%, and even reduce energy costs for the occupants of the finish structure.
Installing Modular Rooms
Who are the customers for these modular rooms? As mentioned earlier, a lot of hotels are made with modular rooms, but offices can have them installed too, since many of the rooms will be similar to one another. A wider variety of rooms, such as bathrooms and break rooms, can also be built and installed like this, not just the offices themselves. Not only that, but some modular, prefab offices are mobile, and construction managers want them. Mobile offices are vital so a construction manager can visit any current construction site to oversee the project, then move again once their work is done. Warehouse managers also need mobile offices, so they can conveniently set up an office in the warehouse floor.
Warehouse partitions can crate new rooms and divide existing rooms with ease, and they can be conveniently set up, relocated, and taken down as needed. Warehouses have ever-changing needs for storage and rooms, unlike most buildings, so these tough, prefab mobile walls and rooms are vital for keeping stock organized in the long run.