All You Need to Know About Induction Forging Furnace
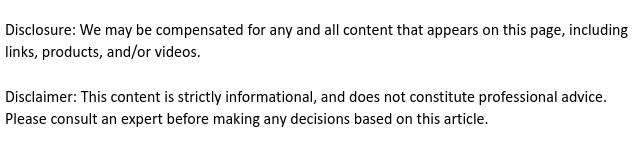
Steel forms an important backbone to almost every other industry out there. It has immensely shaped our society since industrialization and has continued to be an essential component in the automotive, building construction, manufacturing industry.
Approximately 13% of the world’s steel is used in the automotive industry, and up to 50% of the world’s steel is used for buildings and infrastructure. Some 16% of the world’s steel is used for mechanical equipment such as for manufacturing or robotics. Certainly, steel is an essential part of today’s industrial processes.
But how are tools and other products made from these metals? Well, this is either done through the traditional conventional furnaces or induction forging furnaces, which has proved to be a clean and energy-efficient method of metal smelting.
What is an Induction Forging Furnace?
An induction forging furnace is used in steel melting. Unlike a traditional gas furnace, an induction forge pre-heat metals at high temperature before deformation and it offers durable performance with utmost preciseness.
Induction furnace is ideal for small parts as it offers more fitting scale for shaping those small items, without compromising the quality of other parts that makes the product. This is made possible by the fact that the induction heater can heat a targeted part that needs to be shaped while leaving the adjacent parts untouched.
Why Choose an Induction Forging Furnace?
Induction furnace is the best alternative to a traditional gas furnace because of its numerous advantages. If you work in an industry that requires casting metal, then you’d probably understand the benefits of an induction forging furnace. From heating steel with a melting point of 1370 degrees Celsius (2500 degrees Fahrenheit) to aluminum, copper or gold, an induction forging furnace is a great asset, particularly in the precision casting business.
Unlike the conventional gas furnaces, induction forging furnace doesn’t need pre-heat cycles or controlled shutdown, allowing quick metal smelting as soon as it is powered on. The high power density furnace heater ensures the metal component heats up quickly without any lags in the induction melting process.
Another reason why induction forging furnace is good at what it does is efficient heat transfer. Induction heating machine generates heat from within, meaning that less heat gets out and become wasted. Also, it doesn’t produce smoke, hence an environmentally friendly metal melting option than traditional furnaces.
If you are in the metal casting business, you already know that all furnaces are not the same. Aluminum and steel are the two main materials used to make induction furnaces. And they are ideal for metals like iron, steel, copper or aluminum casting.
Most Common Cast Metals
- Gold is a widely used metal for casting. Among other gold uses, jewelry casting is the main one and most lucrative. The process of making gold rings, necklaces, bracelets, and chains involve gold casting, which works best with an aluminum furnace. Generally, casting of gold involves small amounts than of other metals. Therefore you’ll need a furnace that heats up faster ideal for gold smelting.
- Silver is a rare earth metal just like gold and usually is melted in small quantities. This metal can be cast with an aluminum furnace. It’s very efficient.
- Copper is another common cast metal used to make different items. Depending on the amount of copper to be cast, you can either use steel or an aluminum induction furnace. For small quantities, use the aluminum furnace. Large amounts of copper will require a steel induction furnace that is highly efficient in retaining heat.
- Steel is undisputedly the most common cast metal used in many industries. Steel induction forge is the best option when it comes to steel casting. But small quantities of steel can be effectively melted with an aluminum induction forge.
Essentially, without metal melting furnaces, some automotive parts would become a challenge to manufacture and assemble. It would even be a problem to get rid of old car parts that could have otherwise be melted and recycled to make new car parts.