Introduction to Printed Circuit Boards
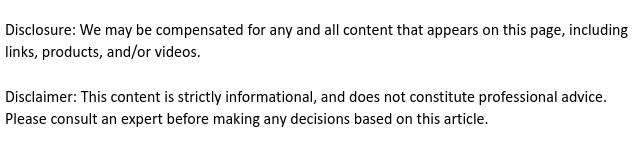

Before printed circuit boards came into existence, circuit boards were made up of point to point wiring systems. These types of systems often experienced short circuits, disconnections, or other failures.
Wire wrapping changed the circuit board industry by tightly wrapping wires around connection points. These were more secure than point to point connections, but were still bulky.
As time went on and electronics production skyrocketed. Subsequently, electronics became more readily available for the average consumer, and there were higher demands for manufacturing companies to compact the size of these products. This lead to the creation of the printed circuit board, or PCB for short.
Instead of bulky or unstable wired connections that were not conducive to the new wave of portable electronic devices, the circuit board has components made of lines and pads, which work to connect device components and transfer electronic signals.
So what goes into PCB assembly? There are four primary components of a circuit board. The center piece of the PCB in the substrate, typically made of fiberglass. This core provides a stable core for the circuit.
A copper layer may be added to one or both sides of the substrate, but most like both. For low quality products that don’t need as much computing power, there will only be one copper layer. These layers contain the connective parts that emit electrical signals.
The soldermask insulates the copper layer and maps the paths for the electrical signals to travel on. The soldermask usually has a distinctive green color, unless otherwise changed by the printed circuit board manufacturer.
The silkscreen is the top layer, that prints the letters and symbols of distinction on top of the PCB, allowing for more comprehensive assembly of electronic devices. These symbols label the function of the PCB connection points.
When circuit boards were developed the price of electronic consumer goods dropped, as PCB manufacturing was a much faster assembly process — despite higher processing powers. A PCB can fit in very small products, which is why products like smartphones and smartwatches are able to exist. Due to the small scales to which PCBs can be produced, they can fit in just about any electronic device.