Putting It All Together, Piece by Piece
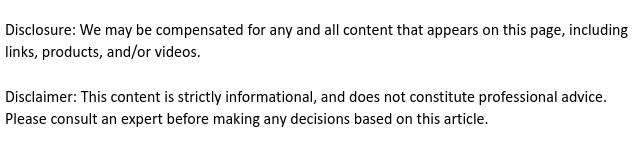

Think for a moment about the development of tools over time. If you consider where we as a species first started out when it comes to the types of tools we fashioned for our use, it is astounding to realize where we have ended up in such a relatively short amount of time. From banging rocks together and learning to sharpen stone and bone edges for piercing and cutting purposes, to the discovery of rounding out a wheel, all the way through the industry boom to today, with the constant whirring of factories run by machines. We use cranes to build towers high into the sky, and heavy duty drills to burrow deep into the earth. And it does not end there.
Breaking down the basics of tooling manufacturing
As our way of life continues to evolve, so do our machines and technology. Most people go about their everyday lives with a basic understanding of the world around them and a point of view that does not much lend itself to thinking about how familiar objects and structures have come into being. Earlier in our collective timeline, things were simpler, and though one may not be a blacksmith or a mason, he or she was probably aware that without those specific set of skills, certain tasks would need to involve the hands of that blacksmith or mason, or carpenter or cooper or tailor. Today, there is not much thought that goes into how things are made, unless you are somehow involved with tooling manufacturing or something similar to the cutting tool industry.
What is tooling manufacturing?
A machinist involved with tooling manufacturing could be involved with any number of steps from the tool engineering at the beginning to the actual manufacturing of a number of different types of items, to the supply of the tools to a specific machine or company, keeping track of a tool management system. These machinists will be able to look at the schematics of a machine or the tools needed for a machine and set to work building those pieces. There are actually quite a few different categories within the industry of tooling, and the quality of work put into each of these categories can directly influence the quality, pricing, and length of service life for the resulting machine.
- The categories of machine tooling
- Fixtures
These are fixtures meant to secure or support a piece in place while it is being worked on to increase efficiency and uniformity. - Jigs
Similar to a fixture, a jig will secure a piece that is being worked on or another part of the mechanism, but will remain stationary instead of conforming itself to the piece. - Gauges
These are tools that are used with others in order to take measurements and display the resulting information. - Molds
Molds are materials with a specific shape hollowed out that liquid can be poured into, which will then harden and set in that shape. Materials like glass, plastic and metal can be used in molds. - Dies
Similar to molds in that they have a specific shape or pattern, dies cut and shape different elements using a press. They can be quite complex, consisting of many parts including several different plates, punches and blocks. - Cutting equipment
Basically exactly what it sounds like, a cutting tool is used to deform or change the shape of another material. It must be a stronger and harder material than that which it is meant to cut.
The next time you see a complex machine in motion, think about all of the little pieces that must fit perfectly together in order to make the whole thing work smoothly. There are numerous devices around us in everyday life that we could probably thank a machinist for having a hand in putting together.