When’s The Last Time You Had Your Workplace Checked For Safety?
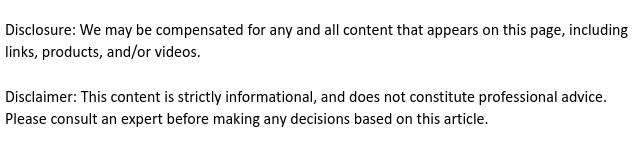

How do you create a conscientious working environment for your employees and customers alike? Some businesses apply for crane training, teaching their workers the ins and outs of useful equipment as they do their daily work. Others prefer signing them up for fall arrest training, detailed seminars that give them the skills and technical know-how to avoid common accidents and work with confidence. Yet more prefer doing their research and investing in quality rigging equipment to get the job done as efficiently as possible. The ideal method? All of the above and more. Safety is incredibly important for both people and businesses alike and a quick investment in round slings or lifting slings won’t do much without the prior proper know-how. Let’s look below at some simple tips on workplace safety you can use for your business at large.
What Is OSHA?
OSHA is an acronym for ‘occupational safety and health administration’, an agency that oversees work environments and reinforces strong leadership roles as well as continuous and conscientious safety habits. A three step process is utilized to prevent dangerous falls and save lives, from providing to planning to training, and can be showcased to employees through rigorous training seminars. There are a few requirements for workspaces that have been established by OSHA, such as implementing fall protection at elevations of four or eight feet. First founded in the 70’s, OSHA continues to lead businesses, employees and manufacturers alike in the fields of health and safety.
What Are Common Safety Habits?
Safety habits are accrued through both physical and mental means, with fall protection courses encouraging day-to-day mindfulness as well as the right rigging supplies like round slings and wire ropes. Wearing the right equipment, such as hardy shoes and gloves with grip, are essential for construction and repair industries. Although companies did not historically require wire rope slings to have identification, recent law changes have pushed for tags to be omnipresent to better be identified by manufacturers and businesses alike. The equipment you’ll need for your particular work space depends on the labor and demands of your industry.
Which Equipment Should I Buy?
The equipment you need depends heavily on your industry and the demands of your brand. Safety nets, to start, are used to lessen fall exposure when working on temporary floors and scaffolds aren’t an option. Generally called fall arrests, these are required if the distance exceeds 25 feet and will ensure that slips or falls are drastically reduced. Sling types, on the other hand, can come in categories of endless, single, two, three or four leg and are adjusted to fit different load types and weights. Last, but not least, lifelines are commonly used in construction industries and special training is needed to use them correctly. Maintenance is essential for equipment to function properly and should be checked throughout the year to guarantee reliability and quality.
How Do I Get Started?
There’s no need to visit your manufacturer just yet. Calling your local OSHA representative and having them give your workplace an inspection will fulfill multiple requirements, starting with any errors your daily environment might contain as well as counseling you and your workers on proper safety habits. After this you will then be advised on ways to improve your establishment, including equipment requirements like round slings, rigging supplies or lifting products. Making schedules to have your business inspected at least once per year will go a long way in establishing safety for your employees. Contact an OSHA representative today and see how they can help you make your business safer today.