How to Ensure Product Quality With Lapping and Abrasives
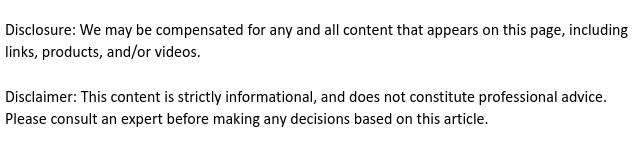

Throughout the production of many industrial goods, there are numerous machining operations involved with the process. Between fittings and construction, countless technologies are used to shape all aspects of a product.
One common and very important machining process comes in the form of lapping machines. Lapping is an action which involves two surfaces being rubbed together with an abrasive material between them. These can be operated manually with hand movements, or through automated machines.
Lapping is used to grind and polish multiple types of surfaces such as glass, gems, metals, or optical glass. Depending on the level of flatness desired, there are different abrasives that can be used during lapping. Such materials as aluminum oxide, emery, silicon carbide, and even diamond, can be rotated between the desired goods to produce varying results.
Using reliable lapping machines are extremely important to the quality of the end product considering how exact the measurements must be. If any of the key grinding components are out of alignment, even by as little as 0.001 inches — 24.5 microns –, this could cause significant consequences to the material being polished. Poor alignment of abrasives and surfaces on lapping machines can contribute to poor quality parts, and overall customer satisfaction.
To ensure the surface accuracy or flatness of these machining processes, a measurement is conducted through the use of helium light bonds. These contrasting lights can measure up to 0.000011 of an inch (280 nm), offering reliable precision. Without a method to determine the quality of a polished product, there is no way to guarantee the consistency of machined parts.
With all of the technology currently in use and in high demand, there are extensive production lines that make use of numerous machining processes, all of which must be extremely precise. From grinding with abrasives, to polishing machines, having reliable tools and machines can be imperative to the success of a business.