High Quality At A Low Price The Growing Popularity Of Modular Offices For Businesses
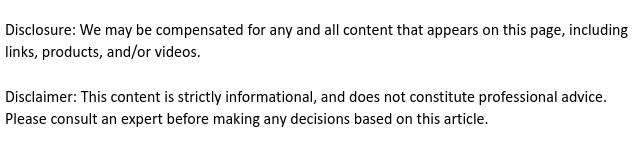
Using space wisely is a function of life. We do it to keep our homes free from troublesome clutter, we do it to save time searching for our keys. It only stands to reason this would extend to business.
Businesses small and large are doing their best to figure out how to get the most with very little. This isn’t just involving marketing, either. Modular warehouse offices are widely considered the most cost-effective means of housing employees and stretching out a brand to each corner of the state. Not only can they be built incredibly quickly, they still maintain a high standard of quality for both customer and worker. If this sounds like something you’d be interested in, read on.
The modular office building is here to stay.
Construction is an expensive feat…and it’s not just the labor that’s costly. Materials, such as brick and wood, can seriously rack up costs that can be hard to reverse even months down the line. The United States today is seeing a surge in eco-friendly construction methods to help save businesses money while still providing customers with good service. You don’t have to worry about recycling materials or smart location, either. Modular warehouse offices are your most flexible resource.
First things first…in plant offices are fast. Modular methods are designed to offer speedy construction times while still maintaining a high standard of quality. One Chinese modular construction company, for example, built a 55-story building in under three weeks. A recent report by the Building Industry Association Of Philadelphia estimated going modular can shave your construction costs by 10% to even 20%. It saves on labor, it saves on materials, all to give you the best of all worlds.
Just how far does the eco-friendly standard go? Modular constructions reduce energy consumption during the building process by 65% or so, also reducing energy costs later on for its occupants. According to studies by UK-based WRAP (Waste And Resources Action Programme) modular construction also significantly reduces waste materials by as much as 90%. Concrete, wood pallets, and cardboard are some of the more obvious ones. You can also see bricks, timber, shrink wrap, plasterboard, and certain types of metals reduced, too.
Just how good does the portable office wall get? Modular warehouse offices can be installed anywhere and maintained easily. You don’t have to worry about taking up too much space or building in an area you’d rather circumvent. FMI’s Prefabrication And Modularization In Construction Survey back in 2013 found up to 40% of contractors considering prefab construction to be part of their strategic initiative. In plant offices give everyone something to cheer about, even if it’s something as basic as convenience.
You choose an industry, you can bet modular warehouse offices have been used at some point. Around 90% of engineers and 85% of contractors have used prefab construction processes on at least some of their projects. Back in 2011 it was found modular construction was rather popular for certain commercial applications, with 50% of respondents to a survey saying they used prefabricated office walls for healthcare facilities. Another 40% used them for dormitories and college buildings. This is only going to get more common from here.
Jump on the bandwagon. Look into in-plant modular offices next time you want to save money and enjoy some extra convenience.