The Development of Welding and Welding Gear
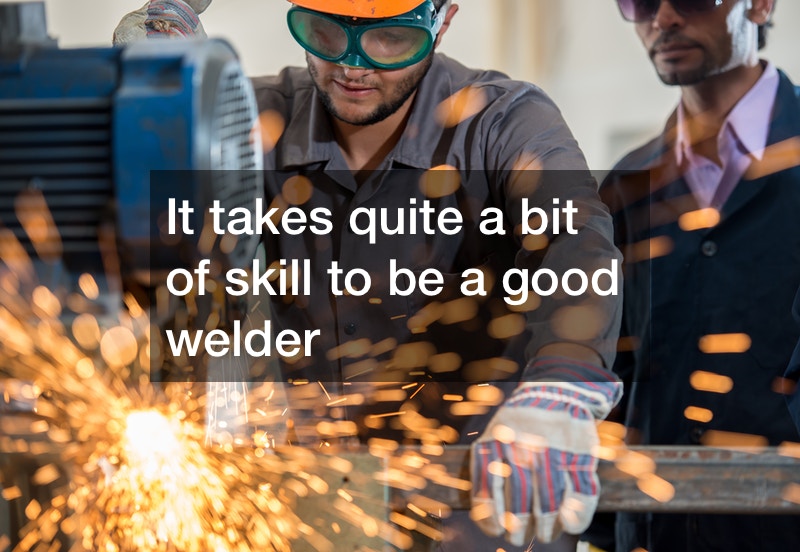
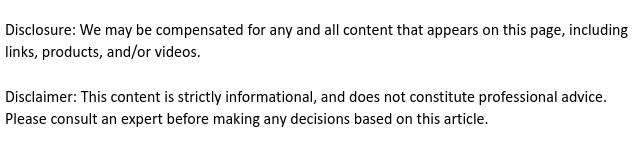

Updated 4/25/22
Welding and fabrication are often used interchangeably. But whereas the meaning of fabrication work is creating a complete metal product, welding is a single process within fabrication. They both involve joining metal together, but a fabricator is a metal fabrication manufacturer because he both designs and creates.
Anyone wondering how to become a fabricator should know that many employers need at least a GED certificate or high school diploma. After that, many fabricators join industrial apprenticeship programs where they can learn on the job, but it is also helpful to attend a vocational school.
Both welders and fabricators can have a similar basic educational route, but to offer fabrication services, one will need to understand technical drawings and blueprints, use metal fabrication software, and have a fair bit of aptitude for math (algebra, geometry, and trigonometry).
In general, the duties of a welder and fabricator will overlap in many ways, but more will be required of the fabricator.
Apart from technical know-how, communicating well with others will yield better results as you will most likely be working in a team.
Many people might be confused about what welding actually is. Welding is actually a very interesting process that involves joining together two metal pieces in many cases. Sometimes, the pieces of metal will both be made of the same material, and sometimes it will actually be two different metals. It takes quite a bit of skill to be a good welder, and people need to be very mindful of safety when they are doing this as well. If you need a welding project to be done, it would be a good idea to leave this to the professionals, rather than trying to tackle it on your own. If you do it on your own, you could end up putting yourself in a great deal of danger.
If you are interested in becoming a master welder yourself, whether you want to do it professionally or just as a hobby, it might be a good idea to talk to a personal welder to learn about how you can do this. You might learn some information about school welding training. This individual might also be able to tell you about small welding tool welder deals, which can be useful to you as you start your journey into the world of welding.
The history of welding and welding gear is the history of civilization. The act of welding itself is essential to all kinds of industry and manufacturing. Welding gear has evolved as welding techniques changed, and milestones we reached in the development of welding affected every area of life. Whether you’re a professional welder taking a break from picking up welding gas bottle refills or just interested in history, here’s how welding and welding gear have developed.
The Early Years

The first examples that we have of welding come from the Bronze Age. These simple welding techniques mainly worked with soft metals, such as gold. This type of welding was known as pressure welding and used pressure rather than heat to bring two joints together. It would be a long time before anyone needed arc welder repair, but ancient peoples in Egypt and the Middle East were able to weld together iron, and welding gear and tools have been found that date as far back as 1000 BC.
Welding and Blacksmithing
During the Middle Ages, blacksmithing would change everything. Blacksmithing used heat to make it easier for pressure to bring two metals together. While pressure was still the primary agent of welding, it became obvious that heat was an important part of the process. This was a big step towards the development of modern welding techniques, gas and gear.
The First Modern Welds
In 1836, Edmund Davey discovered acetylene. This discovery, as well as the invention of the electric arc, enabled the first gas welding techniques. By 1880, carbon arc welding had been patented both in the United States and in England. This enabled people to effectively weld iron and lead, and carbon arc welding was the standard into the early 1900s.
Metal Electrodes
A new kind of welding gear was needed to take advantage of these developments, and in 1890 C.L. Coffin got the first patent for an arc welding process that used a metal electrode to deposit filler metal into a joint. After this, developments came fast and furious. Different types of welding gear included the coded metal electrode, or stick electrodes made of iron wire covered in a mixture of carbonates and silicates. Resistance welding was developed around 1900, and thermite welding made it possible to weld railroad rails together. Gas welding gear and cutting techniques were also finally perfected.

World War I
There was an enormous need for welding because of World War I and the production of armaments. This led to an explosion of welding machines and developments in both Europe and the United States. During the war, the USA had a Wartime Welding Committee Of the Emergency Fleet Corporation. With the war over, committee members realized that developments in welding needed to continue, so they formed the new American Welding Society.
Automatic Welding and Alternating Current
There were some big developments after World War I. Automatic welding was invented in 1920 by the General Electric Company. This new capability was popular with car manufacturers, and the introduction of the alternating current in 1919 eventually affected the welding industry in the 1930s, when heavy-coated electrodes came into use. Stud welding was invented in 1930 at the New York Navy Yard and was used to attach wood to a metal surface. This led to the invention of the submerged arc welding process so that it became easier to manufacture ships. By 1940, gas tungsten arc welding had been refined and perfected.
Post World War II
In the 1950s, two Russian developers were able to use consumable electrodes in a CO2 gas atmosphere. The 1960s saw developments of inert gas with small amounts of oxygen added that provided a new type of arc transfer, as well as the invention of the pulsed current. External gas shielding was no longer needed when the Innershield process was developed, and the automotive industry in the United States began using electron beam welding.
Welding continues to develop, and as it does it provides us with ever more efficient ways of building and manufacturing. Every time it seems we’ve hit our limits, we find a way around and above them. The next time you’re out for air tool repair, consider the amazing development of welding and ask yourself: where could it go next?